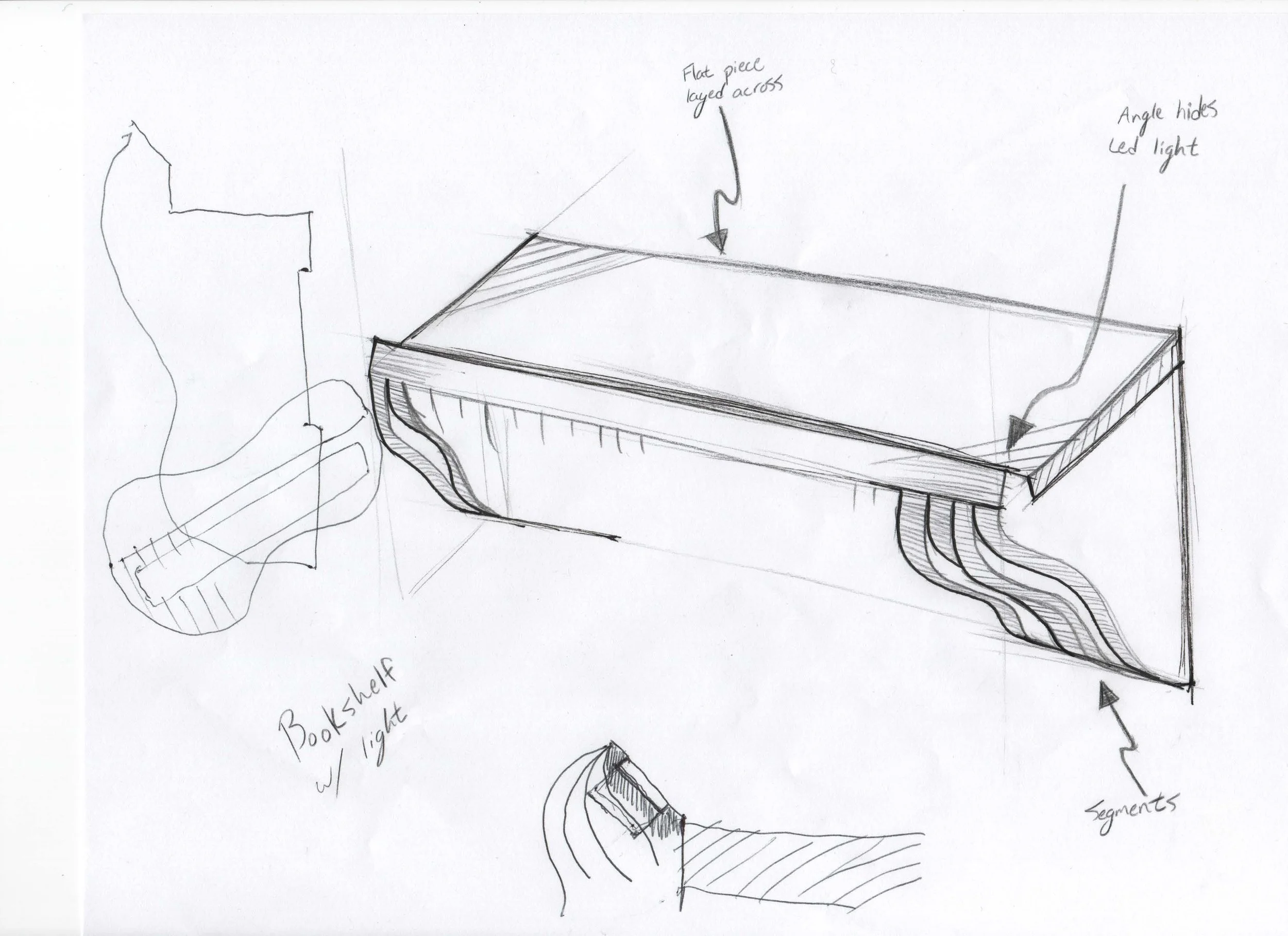
Like most projects, "Mountains" started as a humble sketch. I chose to leave this sketch as-is without Photoshop to really convey how rough this was before it transitioned into the well though out project that it is. The additional drawings surrounding the main sketch were added during a conversation about the idea.

I immediately transitioned into CAD where I created a surface from six different segments and alternated the edges until I was happy with the form. Here, the idea began to take better shape. In the creation of the surface, I determined the width and depth of the shelf based on known requirements for what it was holding and how it would be hung.
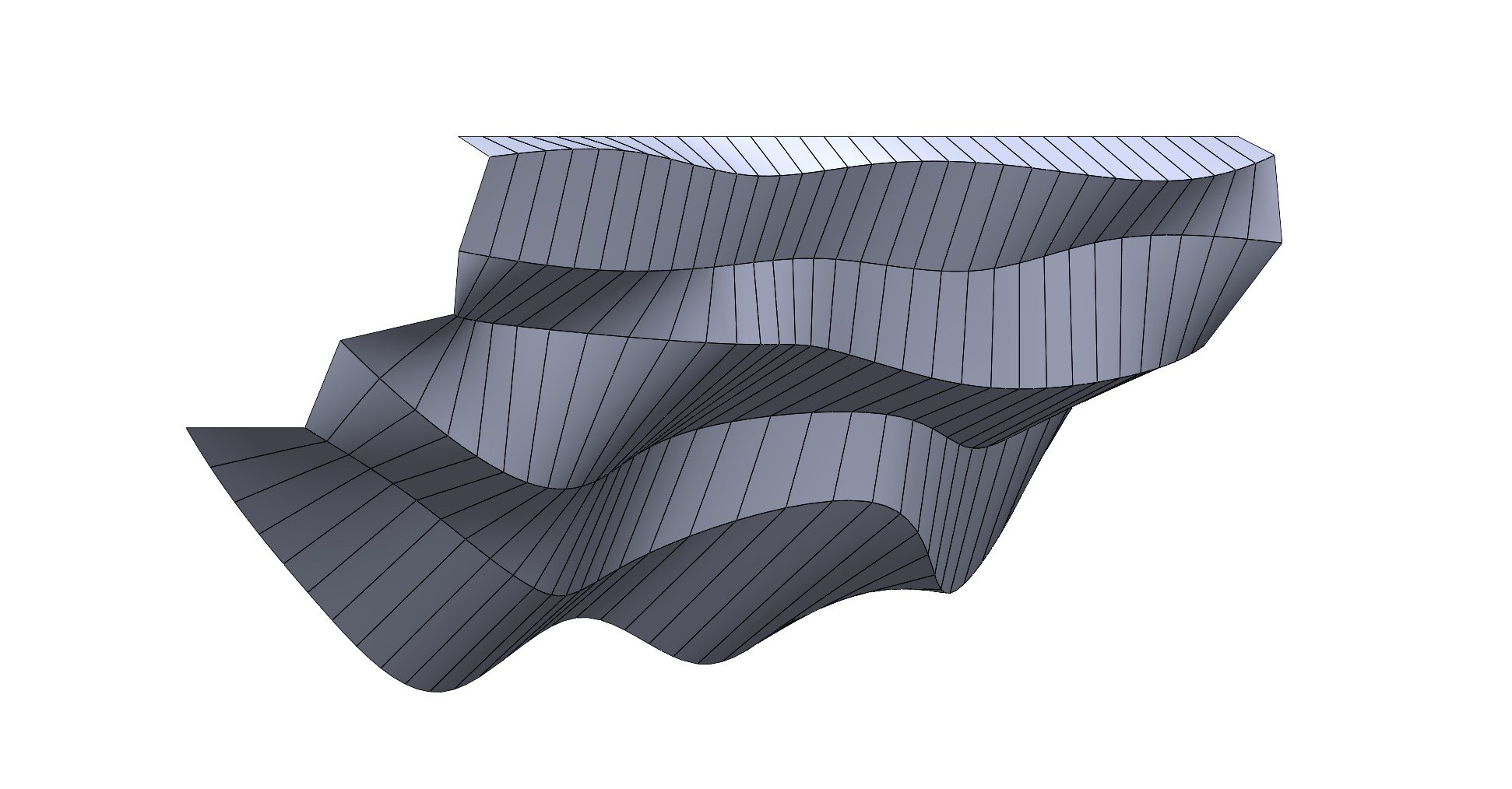
The surface was then split into 32 segments, each the thickness of the 3/4" plywood.

Finally, the original surface was removed and each segment was individually extruded to represent the CNC milled pieces. Here the idea for a French cleat to hold the shelf was finalized.
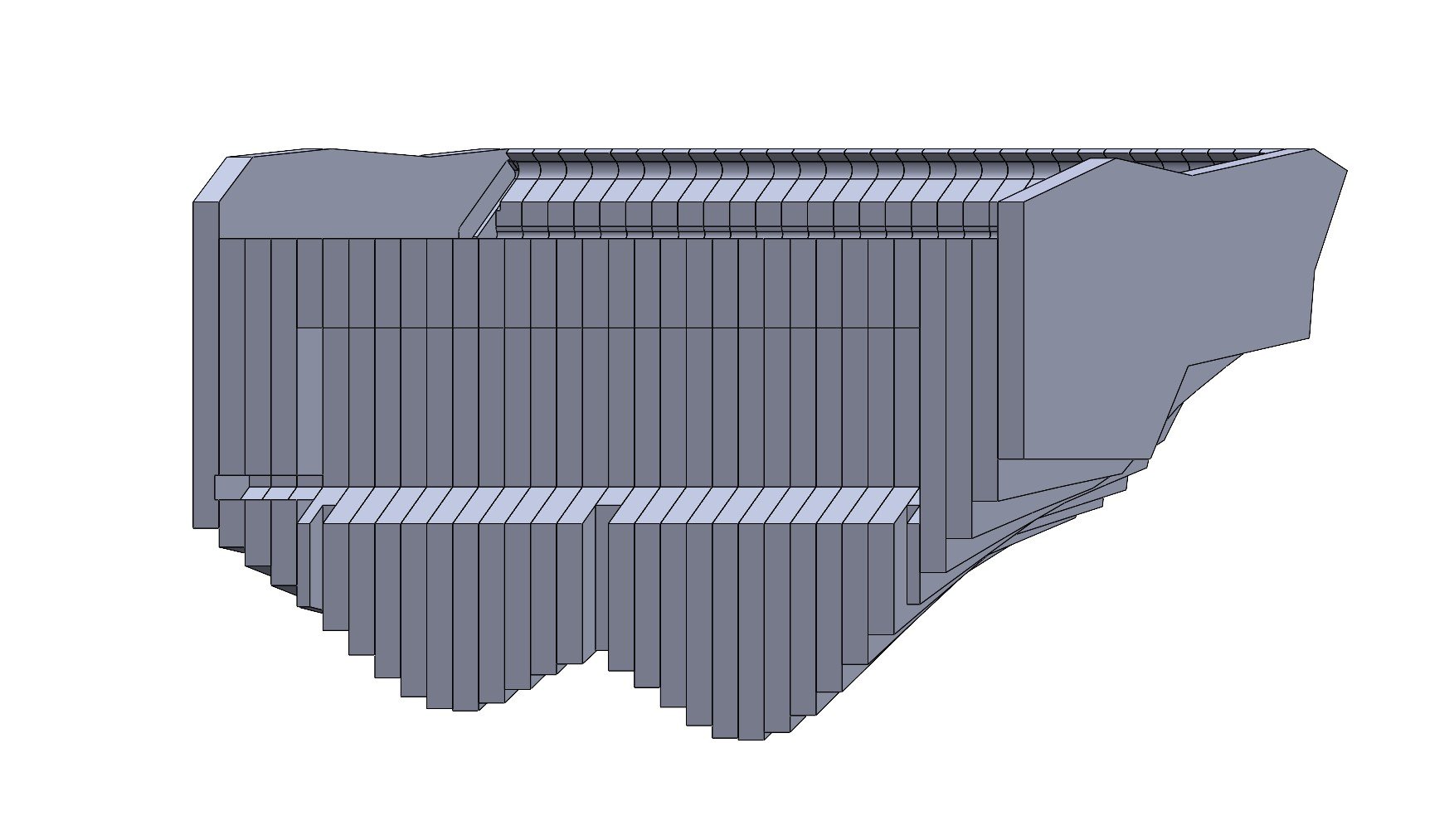
Finishing touches were added to the model, including the slot for the french cleat. At the front of the shelf is a channel for a possible light strip in the future and integrated into the interior and rear are channels for cable routing. Due to variations in thickness, I decided to wait until the shelf was built to take final measurements and hand cut the cleat and top shelf piece.
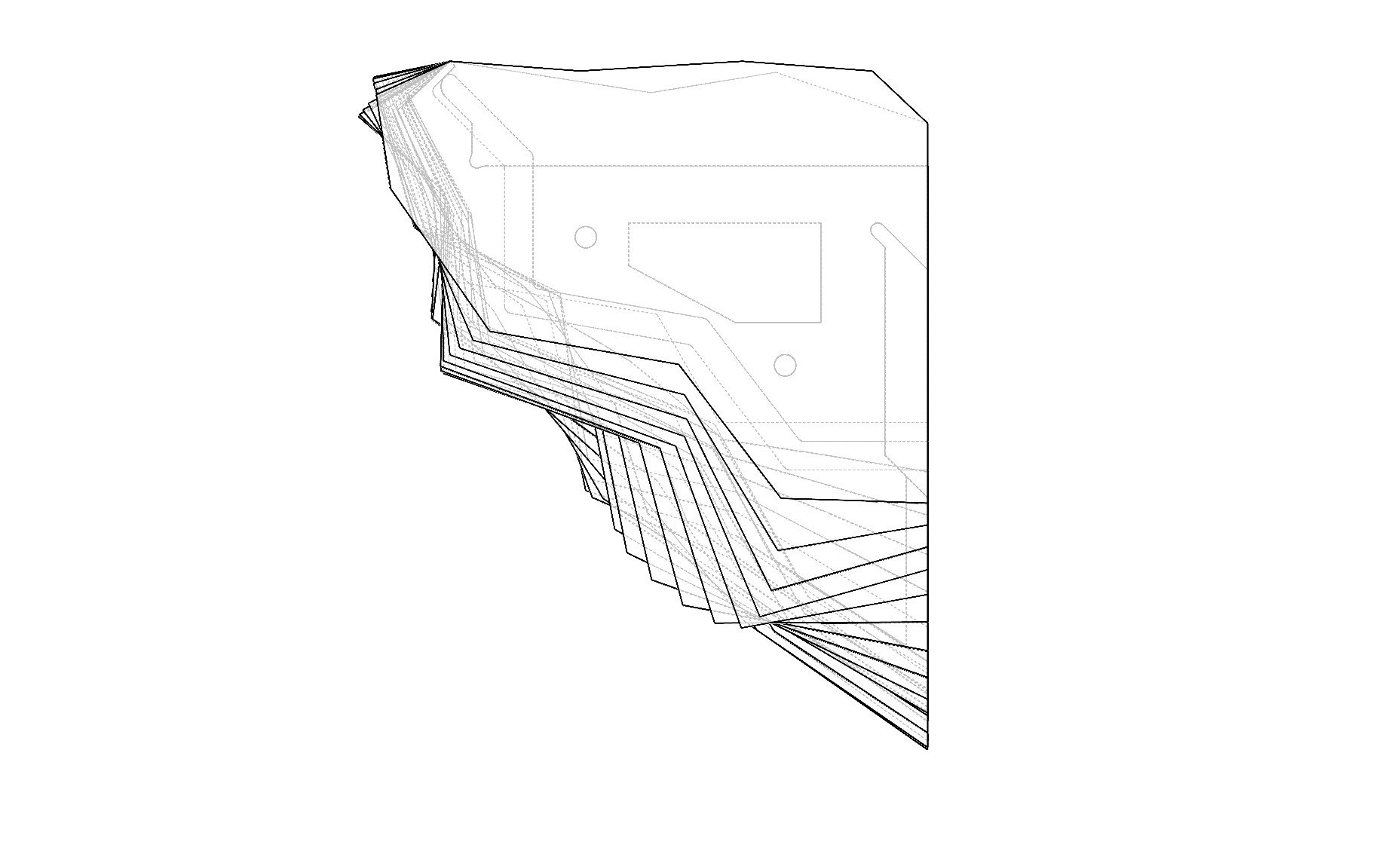
Shown here is a transparent view of the shelf to visualize the interior. A cavity for weight saving can be seen as well as the holes for guide dowels to align the pieces during assembly.
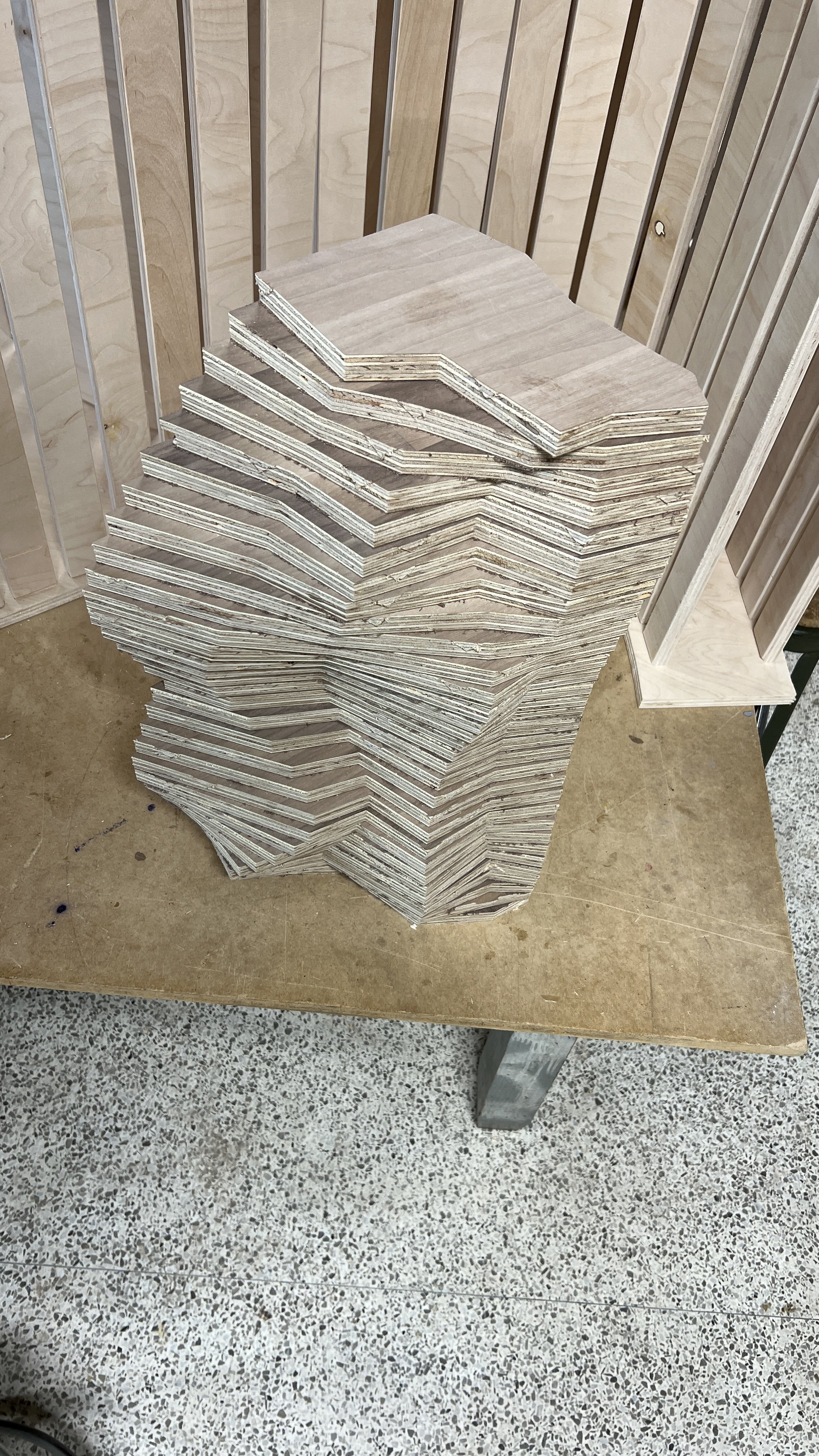
Here is the shelf following the milling process. The pieces are out of order still.
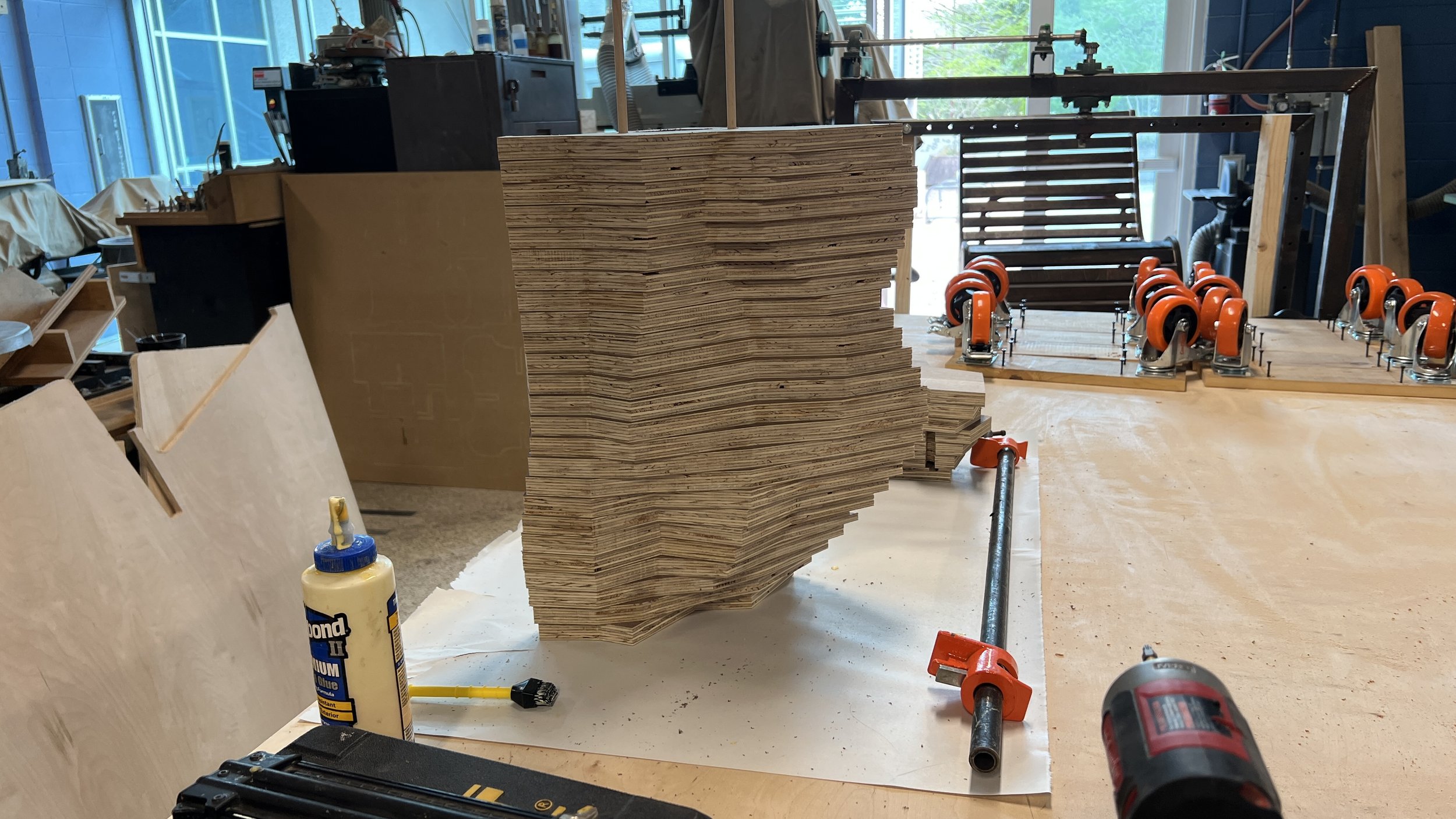
Here are images of the shelf during the final gluing and stacking. A nail gun was used during the gluing process to ensure enough pressure was applied to all of the pieces due to the overhangs in the design.
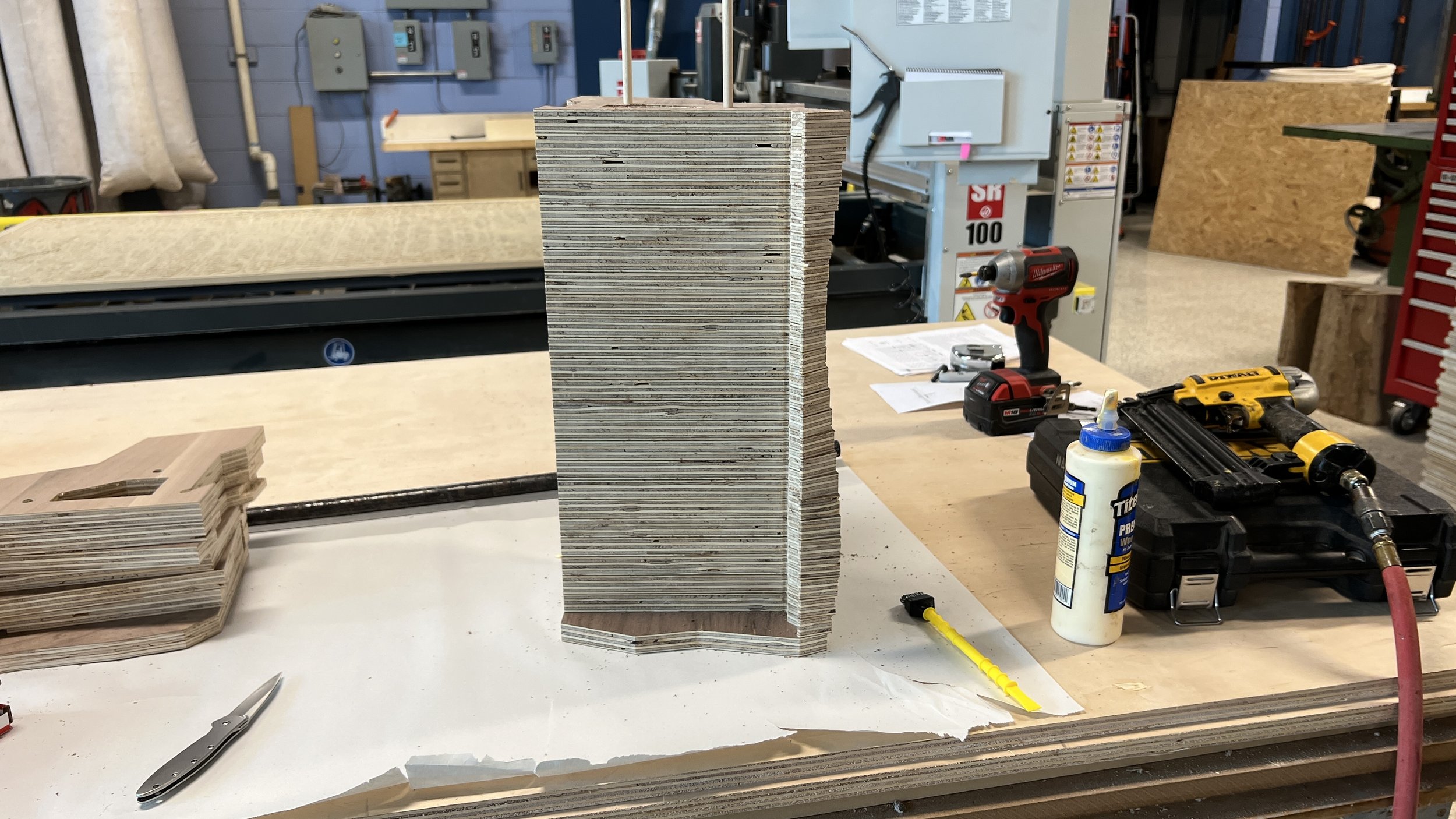
The shelf in these images is still missing the top and coat of Danish oil. All of these can be seen in the final gallery